Comprehensive modelling of engineering fabrics
Most forming simulations for engineering fabrics includes the stiffness along the fibre directions, the shear resistance and the out-of-plane bending stiffness of the fabric. In this project, we develop a novel method to also include both the in-plane bending and torsional stiffness of the fabric [1]. ​The approach, which involves combining beam and membrane elements in a specific way, results in very realistic predictions of the wrinkling response of engineering fabrics [2, 3]. One motivation behind this work was to support the manufacture of low-cost fibre steer structures, in which in-plane bending stiffness clearly plays an important role [4]. Results suggest that for accurate modelling, consideration of both the in-plane bending and torsional stiffnesses is important, when forming flat sheets of engineering fabric into complex shapes.
​
[1] Harrison, P. (2016) Modelling the forming mechanics of engineering fabrics using a mutually constrained pantographic beam and membrane mesh. Composites Part A: Applied Science and Manufacturing, 81, pp. 145-157. (doi: 10.1016/j.compositesa.2015.11.005)
​
[2] Harrison, P. , Alvarez, M. F. and Anderson, D. (2018) Towards comprehensive characterisation and modelling of the forming and wrinkling mechanics of engineering fabrics. International Journal of Solids and Structures, 154, pp. 2-18. (doi: 10.1016/j.ijsolstr.2016.11.008)
​
[3] Harrison, P. and Gonzalez Camacho, L. F. (2021) Deep draw induced wrinkling of engineering fabrics. International Journal of Solids and Structures, 212, pp. 220-236. (doi: 10.1016/j.ijsolstr.2020.12.003)
​
[4] Xiao, Z. and Harrison, P. (2021) Fabric steering technology for variable stiffness panels: manufacture and mechanical testing. Composites Part B: Engineering, 223, 109105. (doi: 10.1016/j.compositesb.2021.109105)
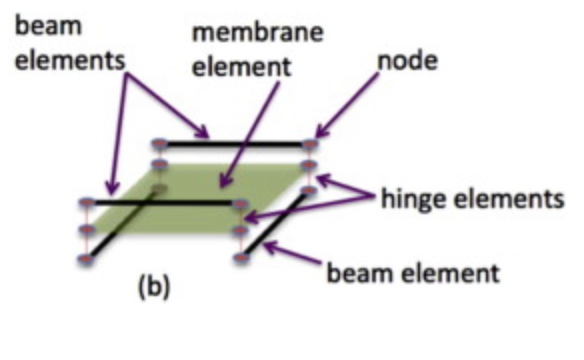


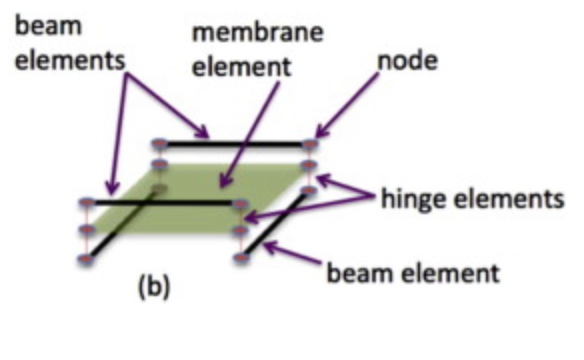