iMelt - induction melt thermoforming of advanced thermoplastic composites
An EPSRC-funded project, the idea is to heat multi-layered, multi-axial laminates, using induction heating of thin layers of tin, strategically placed within a laminate, which is comprised of multiple unidirectional carbon/nylon plies [1]. The tin/composite laminate is contained within rubber diaphragms. Once molten, the hot tin acts as a lubricant to mitigate wrinkles and is squeezed out of the laminate by a pressure driven flow, generated by the action of the press-forming process. The tin's ductility means the effect of tiny amounts of residual tin, left within the laminate, may be beneficial for inter-laminar fracture toughness by mitigating the propagation of cracks [2].
​
[1] Harrison, P. , Campbell, I., Guliyev, E., McLelland, B., Gomes, R., Curado-Correia, N., McGookin, E. and Mulvihill, D.M. (2020) Induction melt thermoforming of advanced multi-axial thermoplastic composite laminates. Journal of Manufacturing Processes, 60, pp. 673-683. (doi: 10.1016/j.jmapro.2020.10.026)
​
[2] Campbell, I., Mulvihill, D. M. and Harrison, P. (2023) The influence of residual tin following induction melt thermoforming of composite parts. Composites Part A: Applied Science and Manufacturing, 164, 107286. (doi: 10.1016/j.compositesa.2022.107286)
​
​
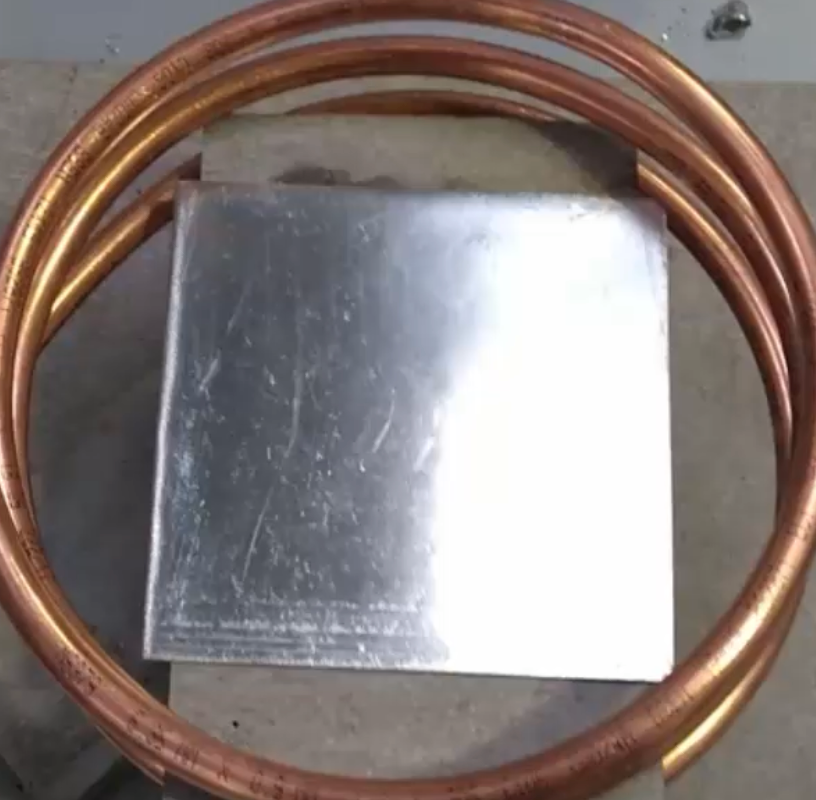
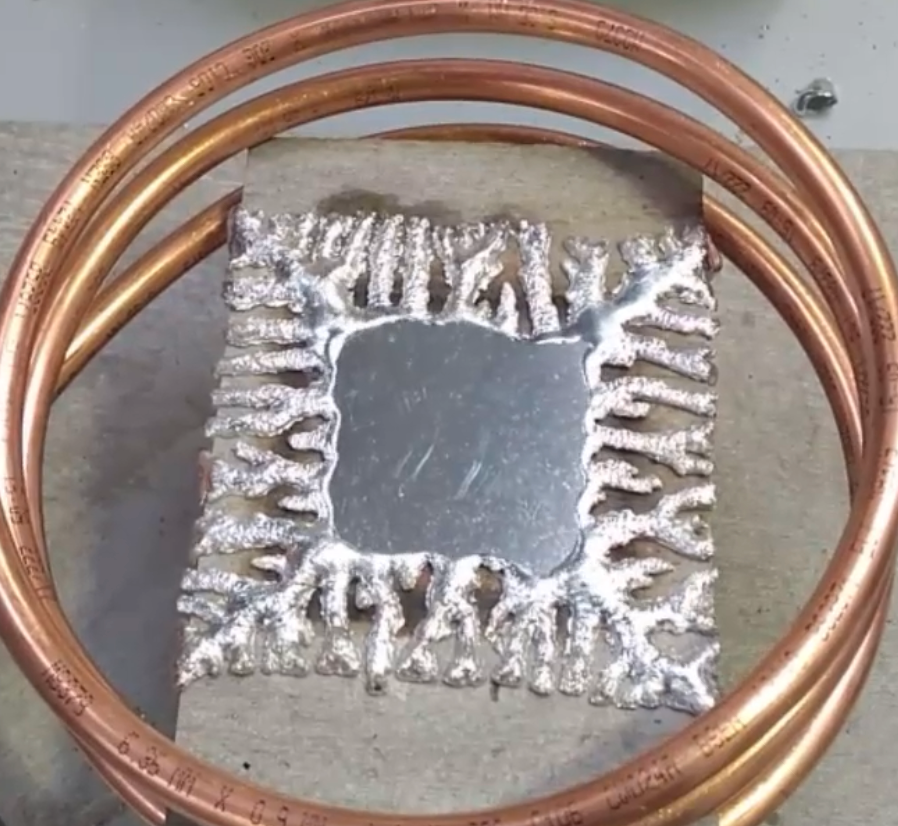

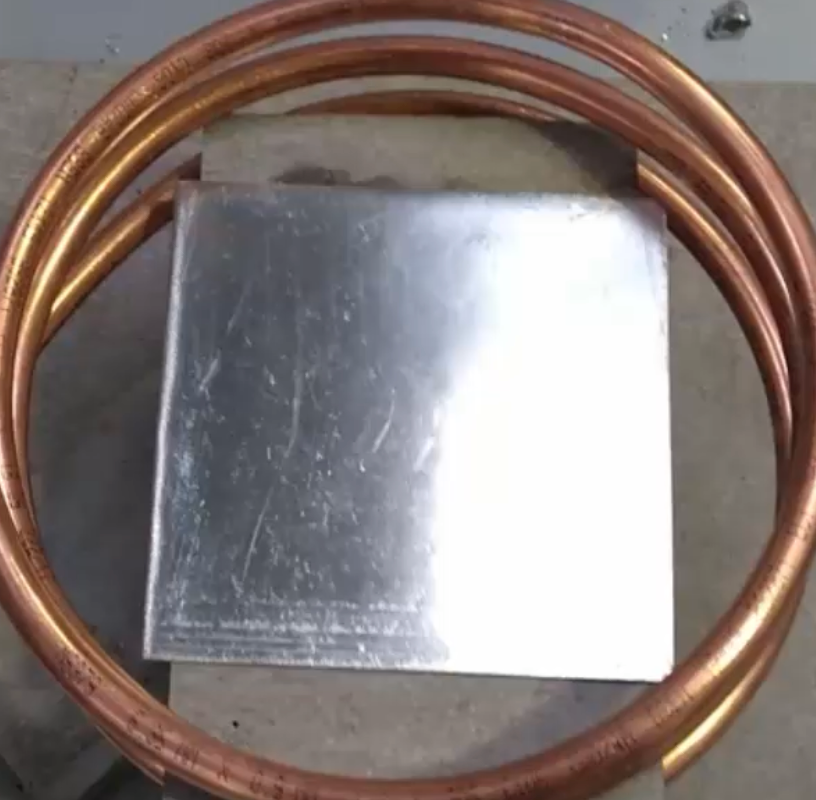